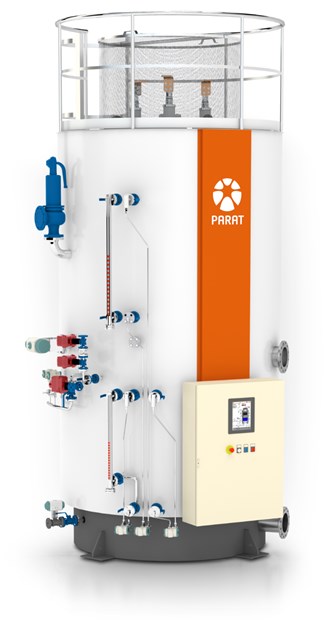
The State of the Art and its Applications
The global energy market is developing fast. Sustainable renewable energy sources like sun, wind, wave and hydro are being utilized at an increasing rate, leading to a re-evaluation of the traditional perspective on energy usage and distribution.
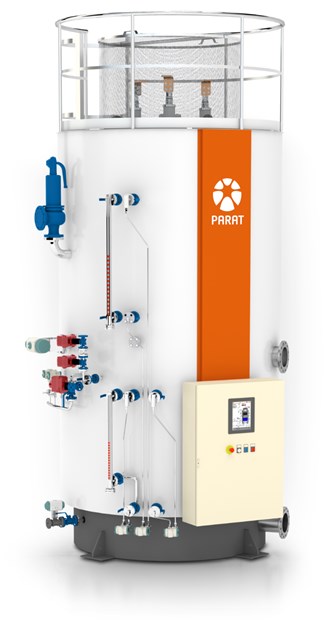
Our modern High Voltage Electrode Boiler brought to the Hannover Messe.
In order to maximize the utilization of the clean energy sources, new technologies come into focus that harness the power independent of the varying demand. One of the most simple, clean and most efficient ways to store energy is by converting the electric power into heat and accumulate it in large volumes of water.
There are two basic ways to convert electrical energy into heat. Either by using low voltageresistance heaters or by high voltage resistance heating. The former is mostly used for capacities up to a maximum of 4-5 MW as the installation cost and equipment size increases almost linearly with the capacity.
The principle behind the technology is to run current through a resistor inside a tubular heating element that in turn generates heat that is transferred to a medium. This means that the capacity of the unit is dependent on the surface area of the immersed tubular heating element. Another potential drawback with this technology is the requirement for a low voltage transformer, additional cabling and power switch boards/effect panels which in turn increases the cost of the installation – and the total space required.
High voltage boilers on the other hand are exceptionally compact, especially for large capacities. The principle of this design is to generate heat by passing current between electrodes that are submerged in water. The resistance generated in the water between the phases creates heat directly in the water.
Parat Halvorsen has a long record of accomplishment for supplying both the aforementioned technologies. The company has done so with great success for many decades. For this article, the focus will mainly be on the high voltage boiler technology. It will offer reflections around this specific product and its possible uses.
A high voltage boiler with 1 x 15 MW and hot water supply at 10 barg/160 °C is in operation at the energy central of ŠKO-Energo, Mladá Boleslav/ Czech Republic. In addition to generating district heating, the capacity of the public electricity network can be regulated via the electrode boiler, thus the new system reduces the risk of blackouts and increases the security of power supply in the country and Europe.
State of the art
State of the art often refers to the highest level of development of a device, technique, or scientific field, achieved at a particular time. In the case of the high voltage boiler technology, this relates to the operational reliability of the unit through its entire lifetime. It is critical to cover three key factors in the design for the product to be of cutting edge.
Firstly, there is the need to control the power flux that again ensures a low current density on the surface of the electrode. If the current density becomes too high, it will gradually eat away the material of the electrode rods, succeedingly worsening the controllability of the boiler unit. A secondary drawback of this effect is the accumulation of metal particles in the water requiring unnecessary blow down cycles to maintain a low conductivity of the boiler water. This is waste of both water and energy and will reduce the overall efficiency of an installation.
Secondly, it is important to ensure a high ohmic resistance between the zero point and earth. To enable this there has to be a sufficient length of insulated material carrying the water from the reservoir to the inner chamber. A correct design will guarantee a very low earth current. A negligible leakage current enables the boiler design to be very compact as there is no need for a protective enclosure around the main boiler shell. The Parat electrode boiler has been measured to have an earth current below 50 mA.
Lastly, an electrode boiler system should be reliable and require a minimum of maintenance stops during the operating year. It should be possible to run the boiler nonstop for a full year with a short two day internal inspection and safety systems check, allowing a 99 % uptime of the boiler system. The Parat electrode boiler complies with all three requirements listed.
Technological applications
High capacity, fast response, compact installation and an overall reliable and practically maintenance free operation is a rare combination of advantages making the high voltage boiler technology a very useful tool for a wide range of industrial and process applications. Below are a few typical examples but the possibilities are numerous.
Backup load
In many traditional boiler room installations, the main heat load is based on oil or gas fired boilers. In case of fuel shortage, maintenance or emergency stops the high voltage electrode boiler can be put online more or less instantaneously due to its fast ramp up cycle. As an example, Parat Halvorsen has installed high voltage electrode boilers as backup heat load in most of the major hospitals in Norway.
Switchable loads
The concept of switchable loads (»zuschaltbare Lasten« in German) – where large scale power consumers can be remote operated by the power companies to utilize available renewable capacity to ensure a proper balance in the power grids without having to turn off the power source – is on full speed towards large scale implementation. The German political government is here in the forefront preparing regulatory changes to make this concept interesting from a long-term commercial perspective and have prepared a legislation to install 2,000 MW of switchable loads in the northern part of Germany.
These installations are to be solely power to heat solutions (PtH) in combination with combined heat and power plants (CHP). The reason for this combination is to double the winning effect of the overall installation. Once again the Parat high voltage boiler is a key component to ensure reliable implementation of these upgraded systems.
2x40 MW installed at DONG Energy in Aarhus, Denmark.
Primary and secondary grid regulation (PRL/SRL)
One of the main requirements for boilers in primary regulation is the ability to ramp up and down from idle to full load in less than 30 seconds.
The high voltage boiler from Parat Halvorsen can offer exceptionally fast turndown and fully meet the requirements for both primary and secondary regulation for steam and hot water systems.
Primary heat source/primary load
It has become increasingly viable to use electricity as the main energy source for heat production in small to medium sized process plants. The practical advantages can in some cases outweigh the differences in the operating costs. Exceptional reliability in combination with clean and compact installations are significant benefits when considering the alternatives.
In Norway, the price difference between electric power and alternative fuels like oil and gas is at times very small. In many cases the electric power is cheaper than the fuel based alternatives.
In the Gulf of Mexico a marine version of a Parat high voltage boiler with 1 x 8 MW and hot water supply at 18 barg/180 °C is in operation at BW Pioneer, a floating production and storage unit (FPSO) operated by BW Offshore.
Offshore process installations
Large offshore oil processing installations normally generate their own power using gas turbines with waste heat recovery. On the northern continental shelf, new regulations are coming into place requiring that the process installations use power from land to reduce the local emissions caused by the traditional gas turbine power plants. The raw processing of crude oil normally requires a significant amount of heat that is traditionally provided by a combination of waste heat from the turbine plants and back-up oil/gas fired boilers.
By removing the local power plant, the process installation needs an alternative heat source. The high voltage boiler is the ideal solution due to the exceptionally low weight and space required for the installation and the high reliability of the system.
Parat Halvorsen has supplied one high voltage boiler to a floating oil-processing unit that has been in operation since 2009. It is very likely that there will be a great number of similar emission free installations realised in the North Sea in the years to come.